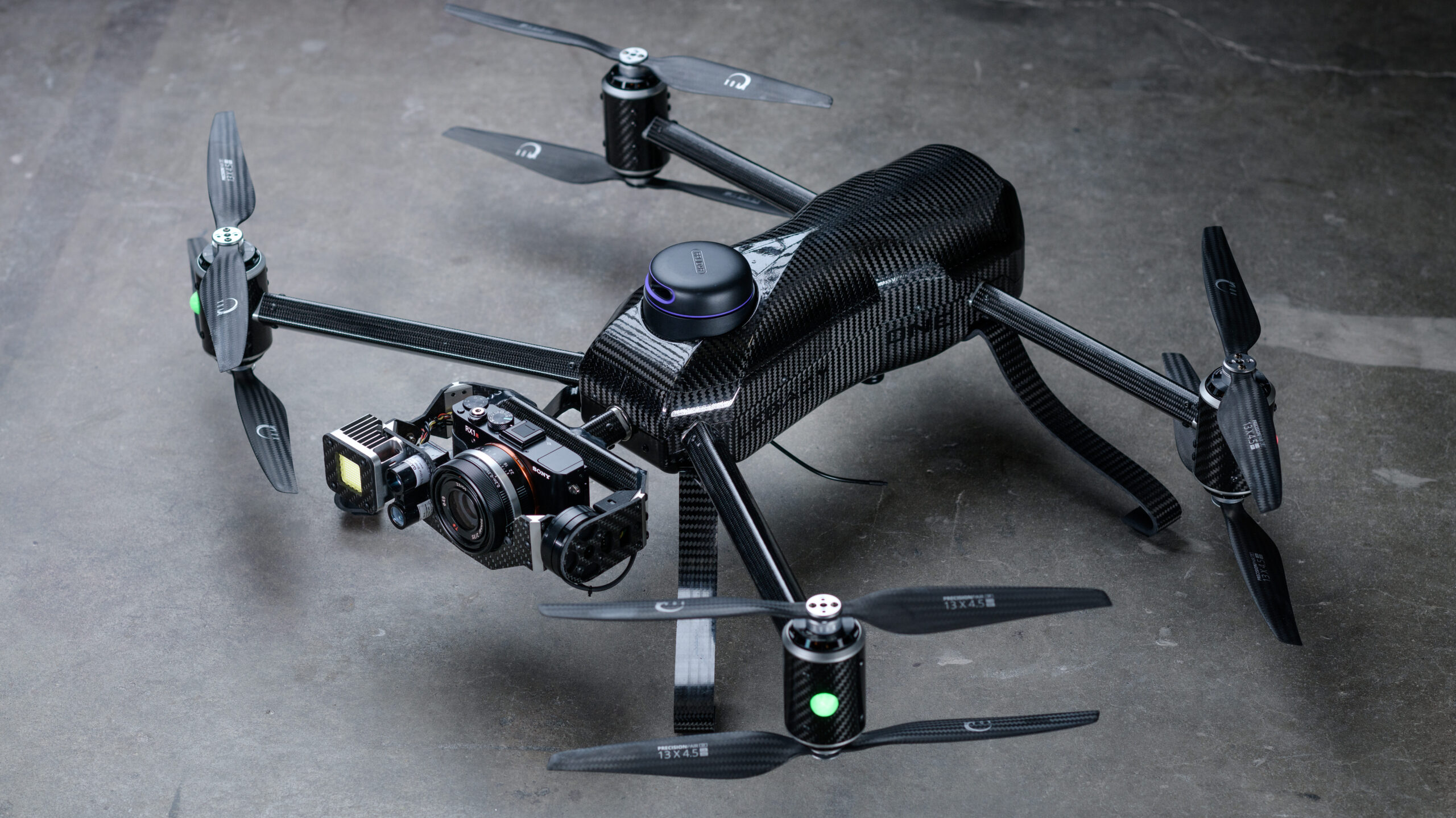
Inspection Drone: The Perfect Internal Flying Machine
The inspection drone was an industrial inspection UAV built for internal confined space and GPS-denied environments. The vehicle is built around a 360° LIDAR with multiple automated flight modes and a high-resolution camera. While we faced numerous design challenges during development, I tried to highlight some of the key designs points which made the inspection drone truly unique.
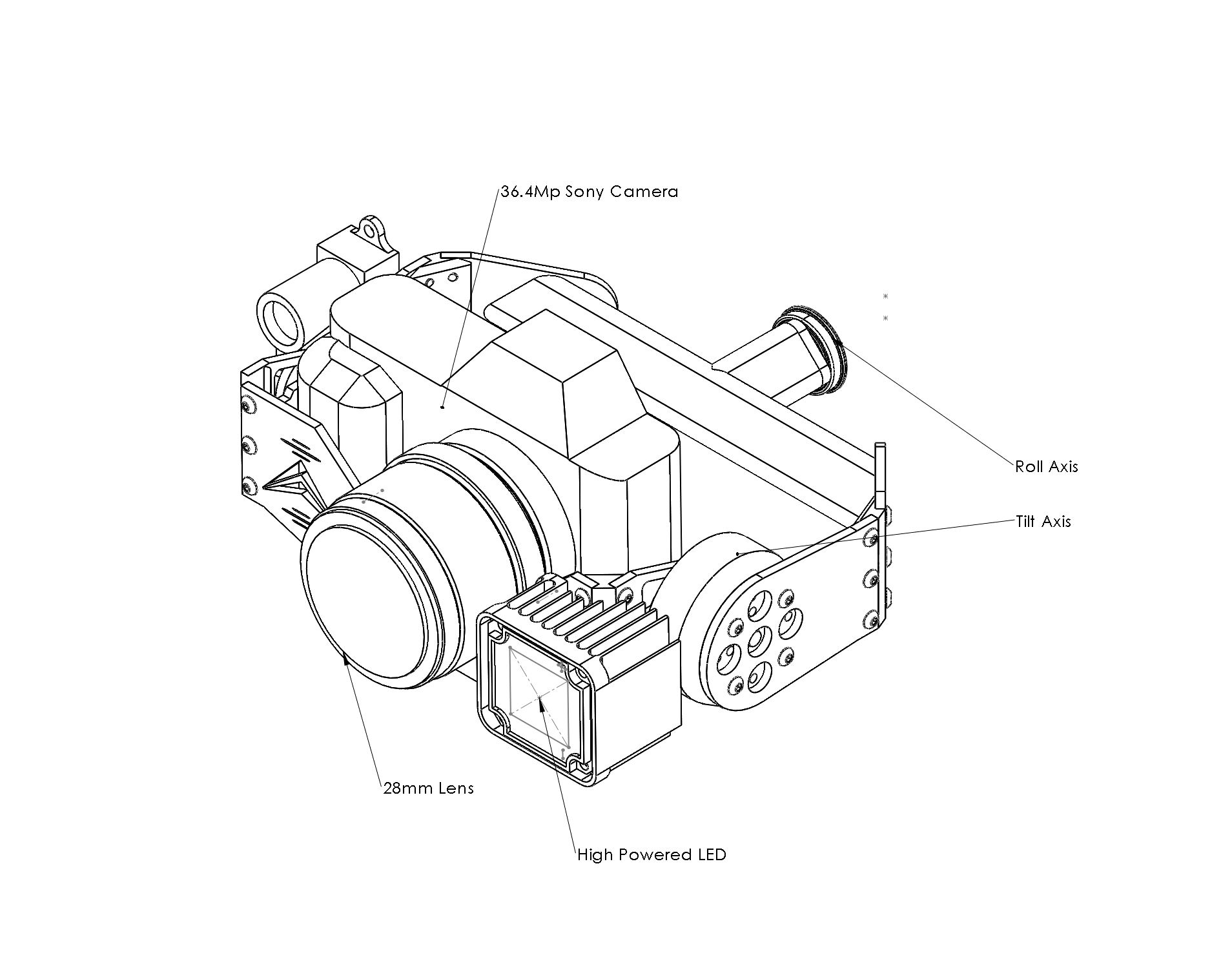
Payload: 42 Megapixel Camera
One of the first areas we focused on during the development was what type of payload the drone would have. Most inspection drones had small cameras not an old iphone. We decided to mount a 42 megapixel camera on the front, allowing the drone to inspect from the ceiling all the way down to the floor. This camera was accompanied by a 10,000 lumen light and a distance capturing LiDAR for inspection measurements.
Size: Perfect For All Manways
Once we had the payload figured out, we had to make sure it was possible to create an airframe small enough to fit inside all manway entries. This proved to be quite the challenge and took many airframe iterations. Ultimately, we settled on airframe design which resembled the letter “K”. This allowed an unobstructed view for the camera payload, while also keeping the frame compact enough to fit everywhere.
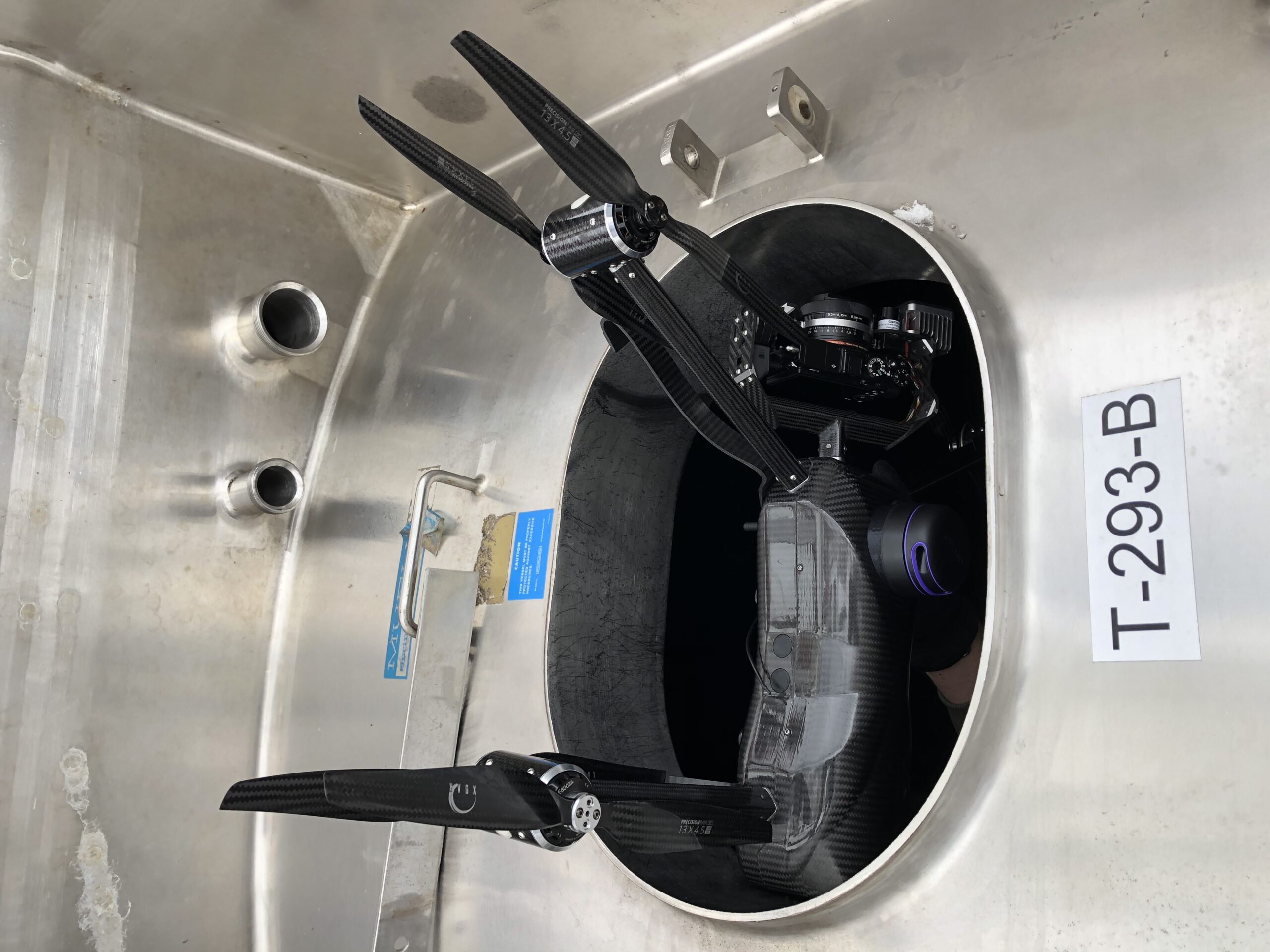
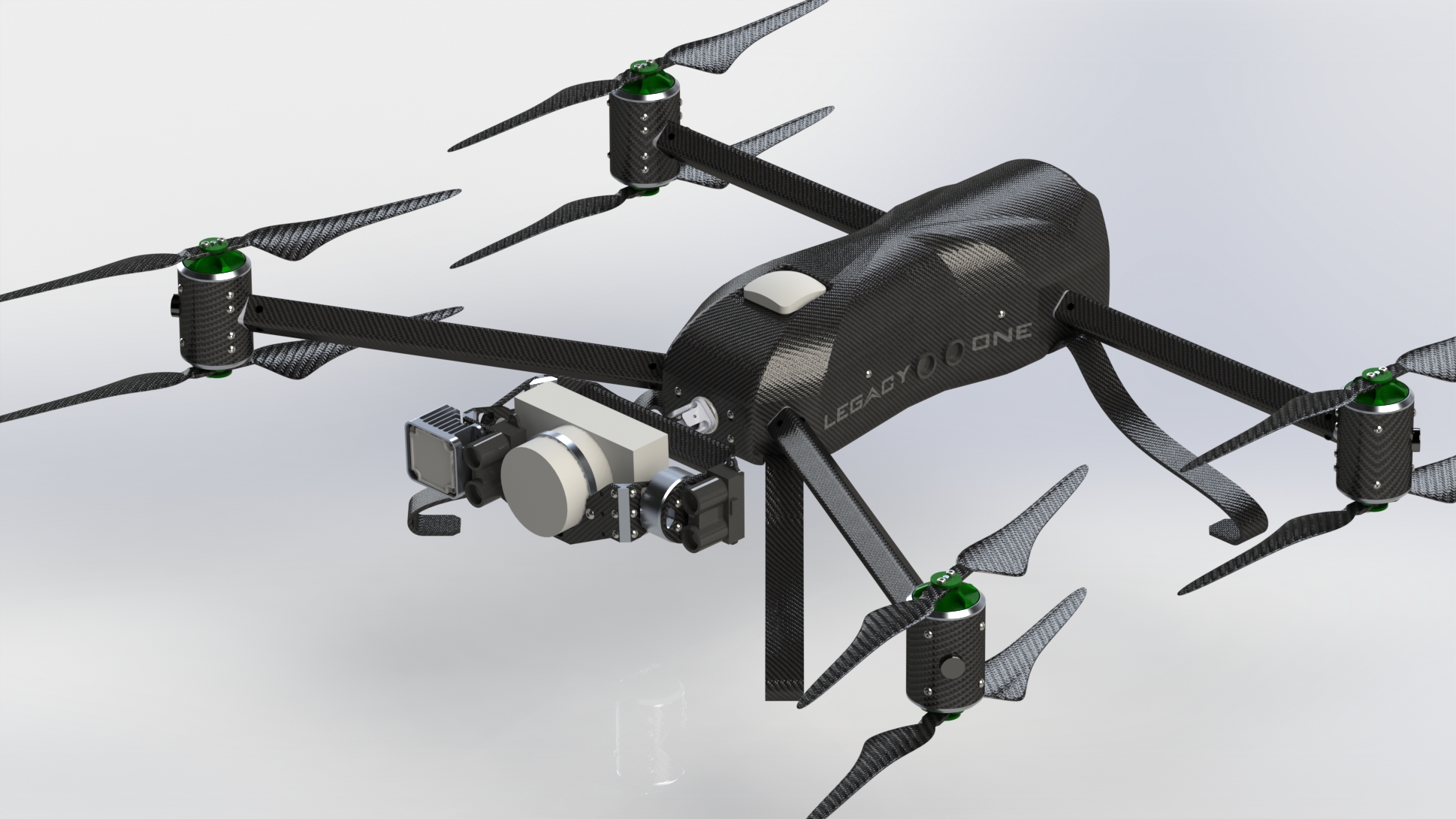
Redundancy: Power In Numbers
Creating a system capable of handling any failure is difficult, especially when the failure might happen while flying. For this reason, we chose to design an 8-motor double stacked power system for the inspection drone. Allowing it to be one of the few drone systems capable of maintaining controlled flight, even during a motor failure.
Transportation: Traveling Without Fees
One of the last and equally as important design challenge was packaging. Being inspections equipment meant the drone would constantly be on the move. Trying to design a “ready to fly” system in a box was the objective. We managed to design a case that was the size of a large suitcase all while keeping the fully packed weight under 50lbs. This is important because it allowed the system to travel on the airlines without paying any oversized or overweight fees. Customers always appreciated not having to ship the equipment ahead of time, potentially risking unwanted and expensive damage.
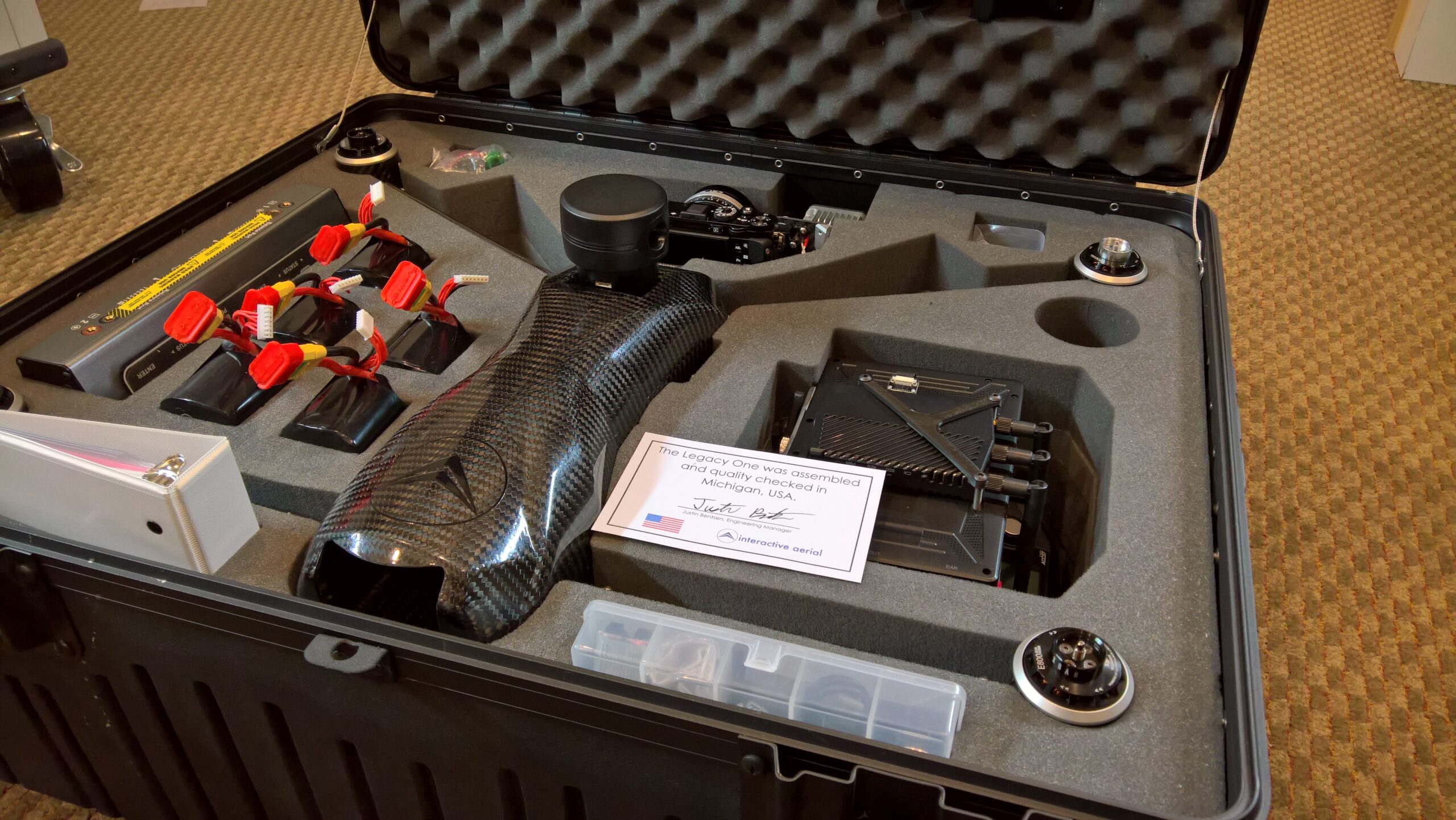
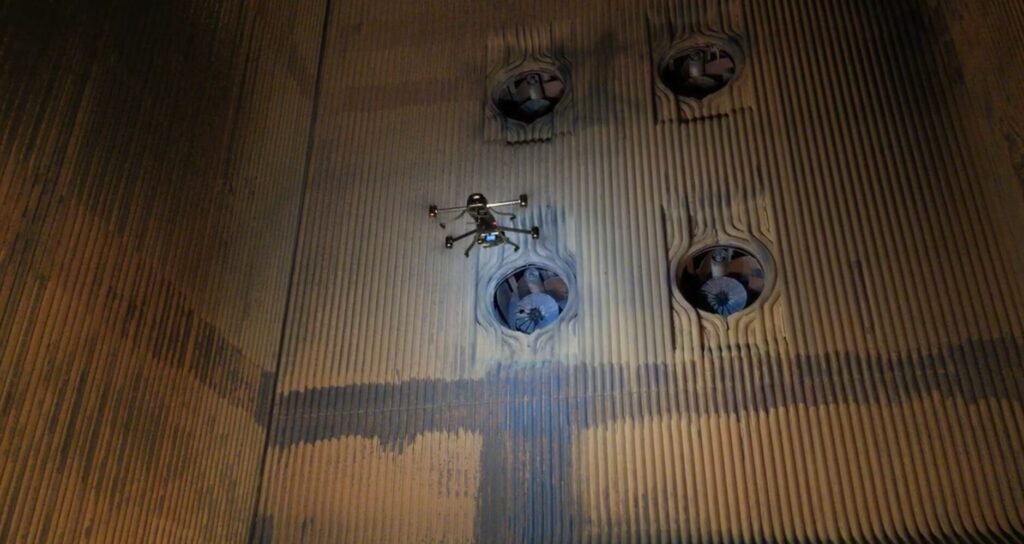
Start Your Project
Don’t miss out on the chance to turn your ideas into reality. Partner with PFM Design today for innovative product development.