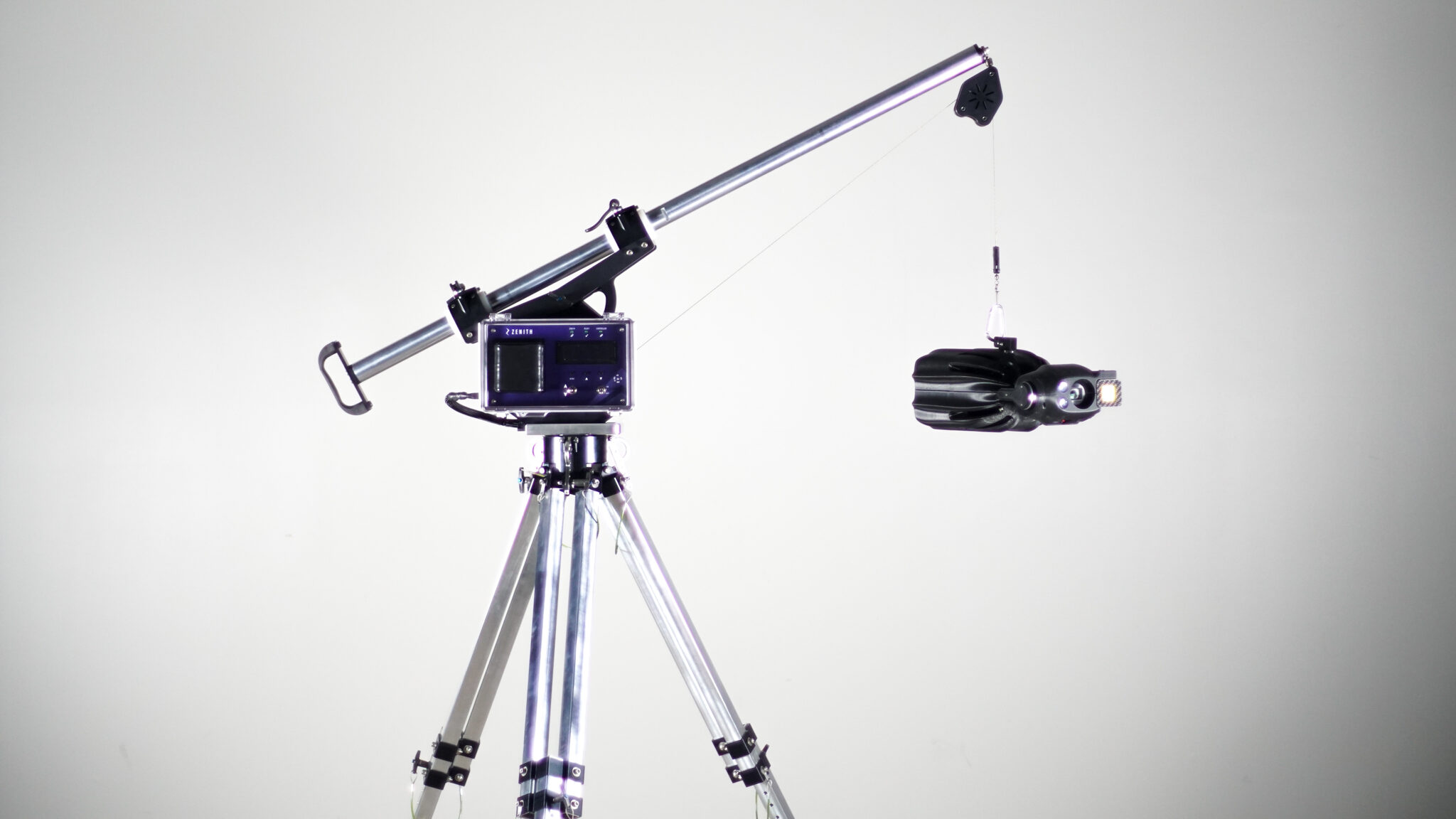
Inspection Camera: Vertical Spaces -Conquered
The inspection camera was developed to allow inspectors to have simple solution to a complex problem. It was developed to allow a single inspector the ability to inspect any part of a tall asset, such as a tall tank. The challenge was to create a system which could adapt to any environment while being simple to operate. for this reason, we chose to design a camera that would repel down instead of a drone which would fly up. the trick was creating a camera unit which was able to control the direction it pointed without needing any sort of rigid mounting system other than a simple cable. That is the magic of what we achieved with the inspection camera.
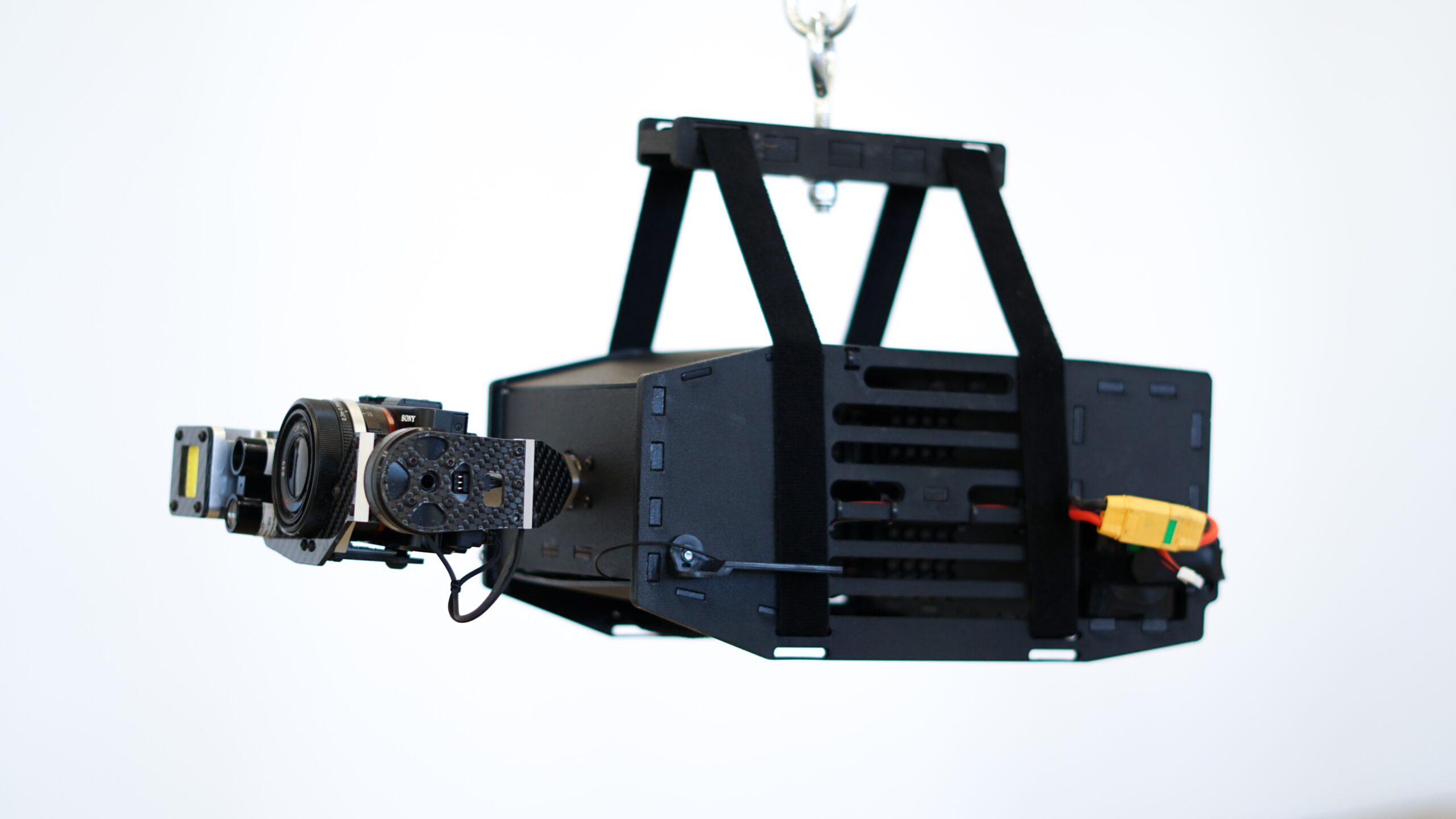
Develpment: Rigidity Through Torque
The early prototypes of the system used the camera unit from the inspection drone. this allowed us to quickly develop a working prototype, proving the concepts viability through use. We also laser cut simple plastic sheets to create a body which gave us space to develop the heading hold technology. We created a system which used grid paddles and spun them with electric motors keeping a rotational torque balance. This was the key to being able to keep the camera pointing in the same direction even if repelling over 100ft down the inside of a tank.
Refinement: 3D Printing
Through continued refinements and product development, we were able to create the commercial units we later sold. These units were made from high strength 3D printed materials. This worked well as it allowed for continued improvements and on demand manufacturing. Each body would take about 24hrs to produce and the complexity of the mold necessary for injection molding would simply be to cost prohibitive for the demand. The roll additive manufacturing played in the success with the inspection camera can’t be overstated.
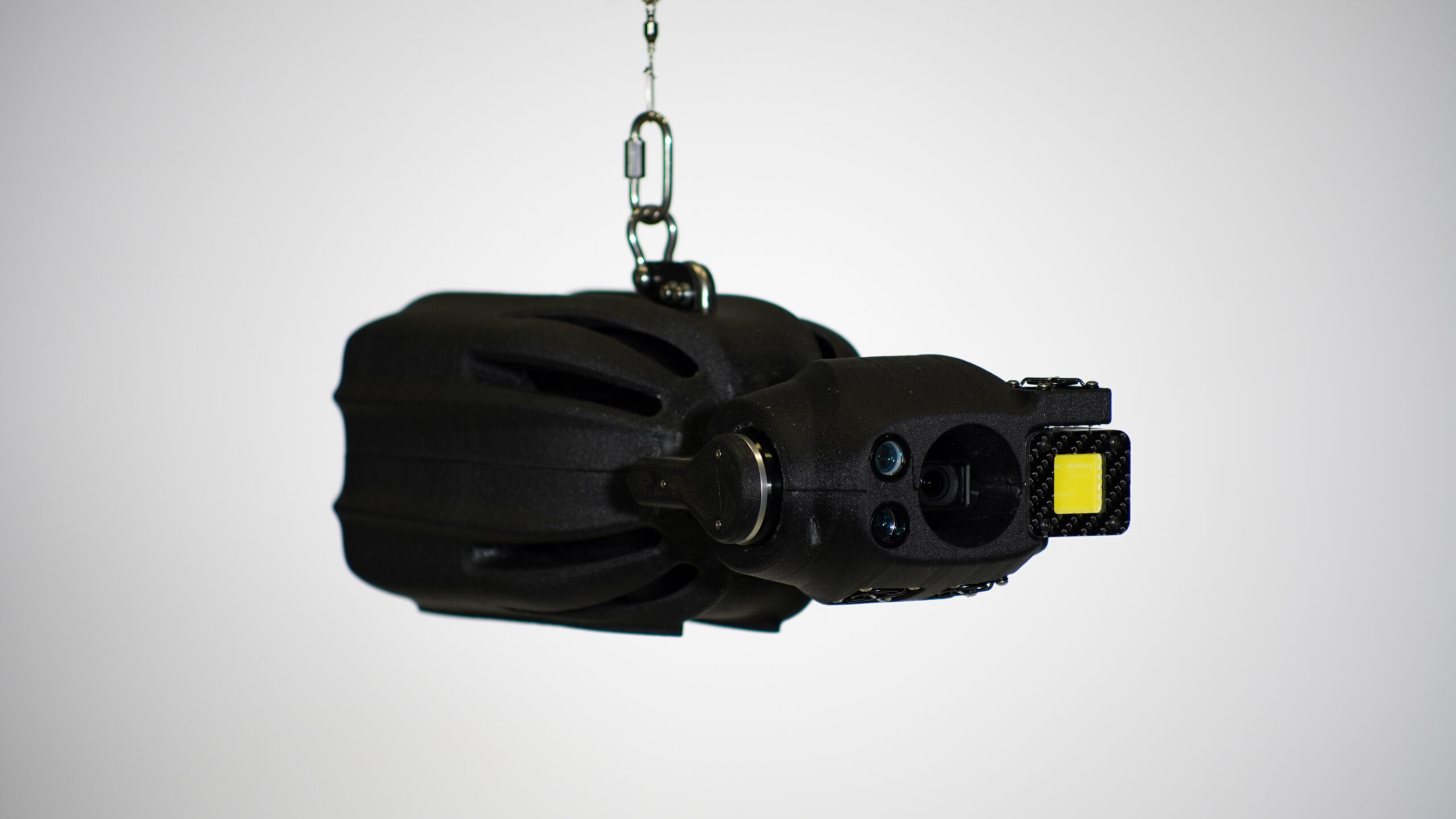
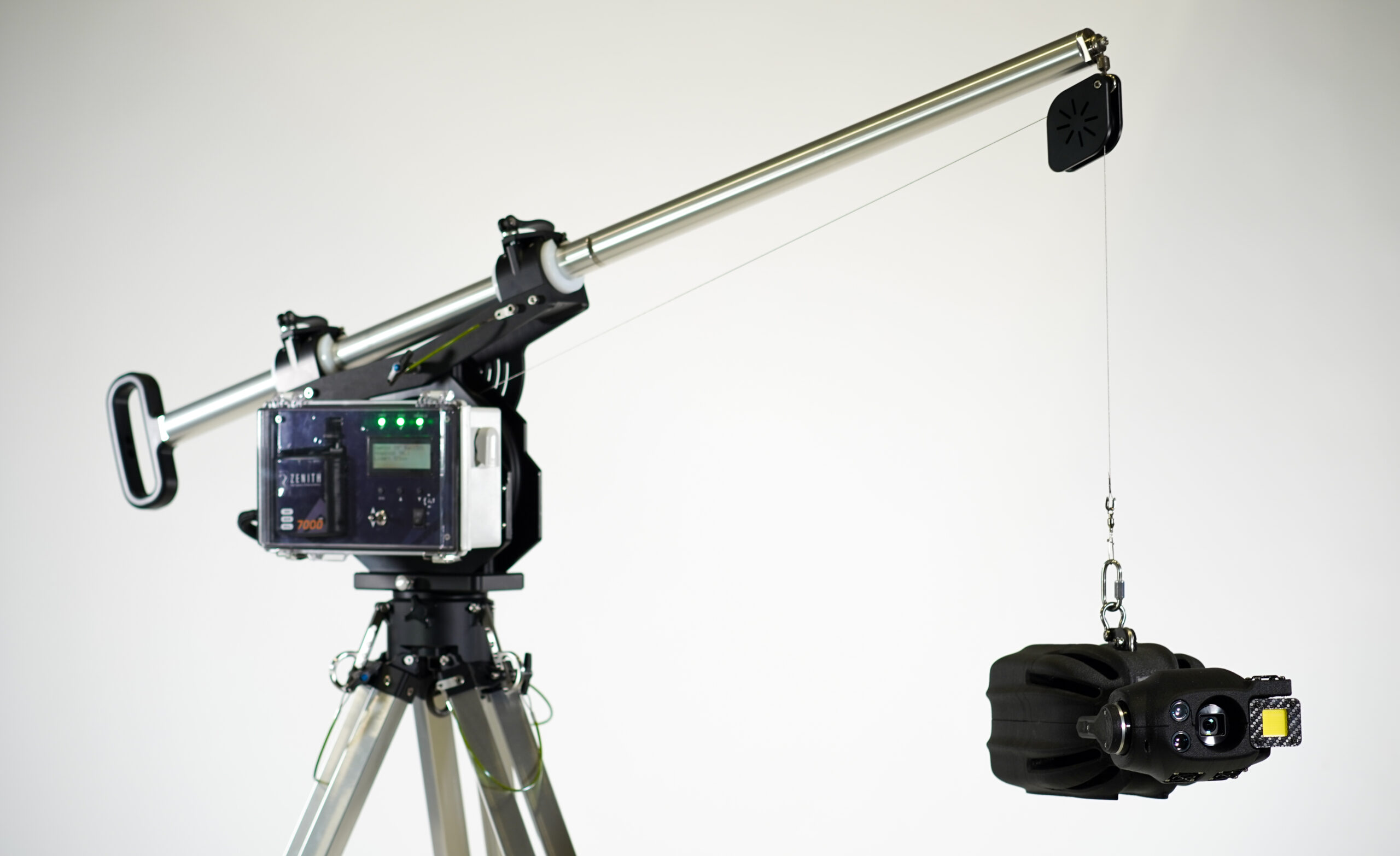
Winch: Up and Down with Ease
In order to control the height of the camera unit, we developed a wireless, battery powered winch system. This system allowed for automatic height control of the camera unit, placing it a wherever the inspector needed. It also had a built-in height encoder giving inspectors the ability to reference height data within the photos, with an added benefit of repeatable inspections year after year. If the electronics box ever failed, there was even a backup rachet system built in, allowing manual retraction of the camera unit.
Tripod: “Do it All”, Compact yet Versatile
The final piece of the puzzle was a safe way to anchor the entire unit. This was important because the extension arms on top could extend out to 12ft. For this reason, we had to do a ground up tripod design. We were able to design a tripod which folded up small for transportation while being large enough and strong enough to take the needed abuse. We also incorporated many tiedown points allowing the tripod to be anchored to any area of the environment keeping the system safe from ever tipping over. The tripod is robust enough one could stand on top without any issues.
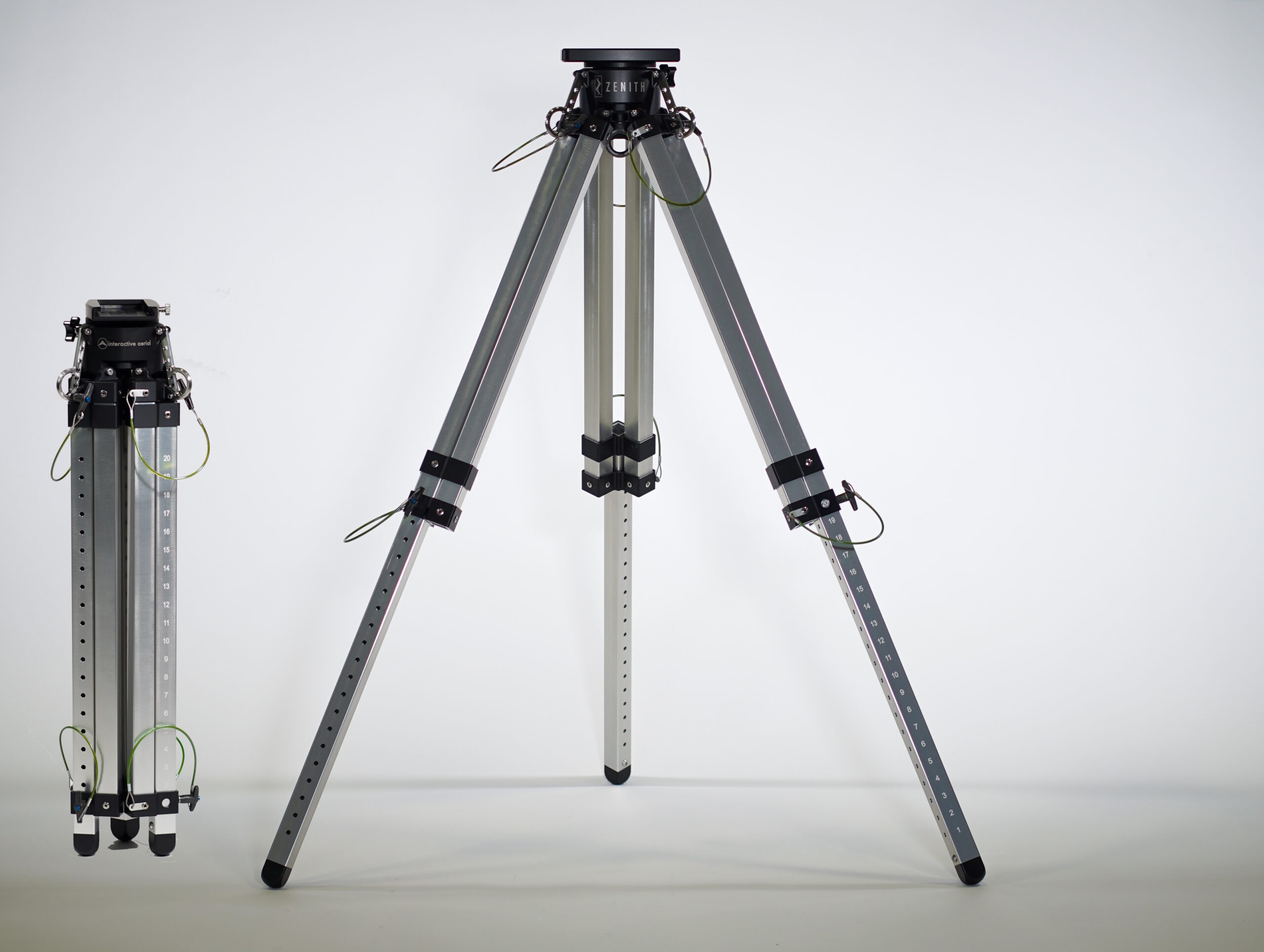
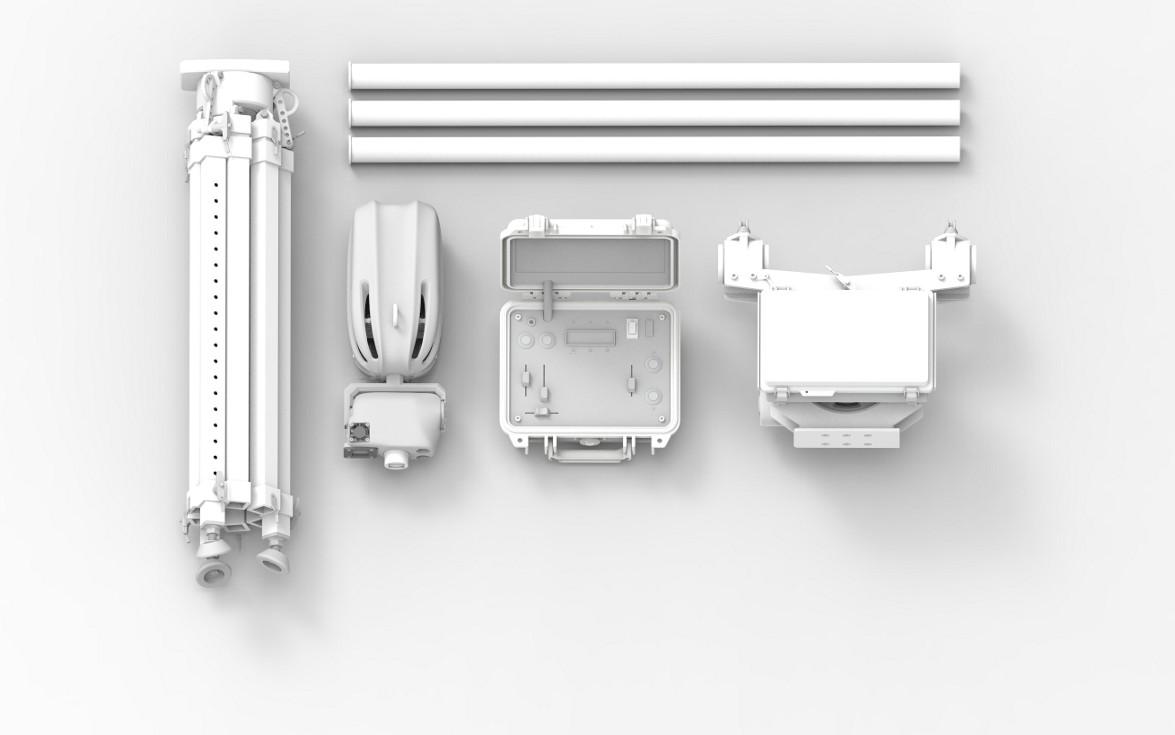
Start Your Project
Don’t miss out on the chance to turn your ideas into reality. Partner with PFM Design today for innovative product development.